Jetway Polyethylene Sheet Roller Chain Wearstrips Chain Plate C100D
Product Display
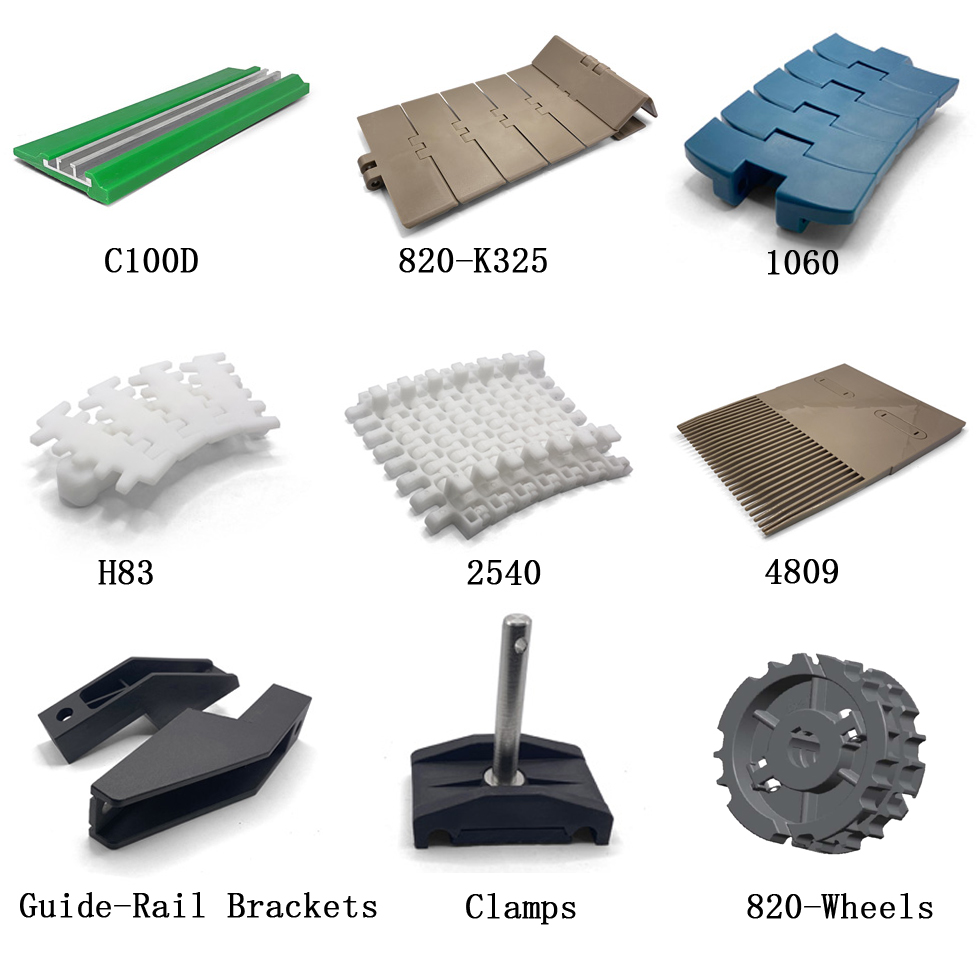
Quick Details
1.Luohe Global modular conveyor belt has more than 10 times service life,long life time and reducing replacement cost than traditional conveyor belt.
Applications
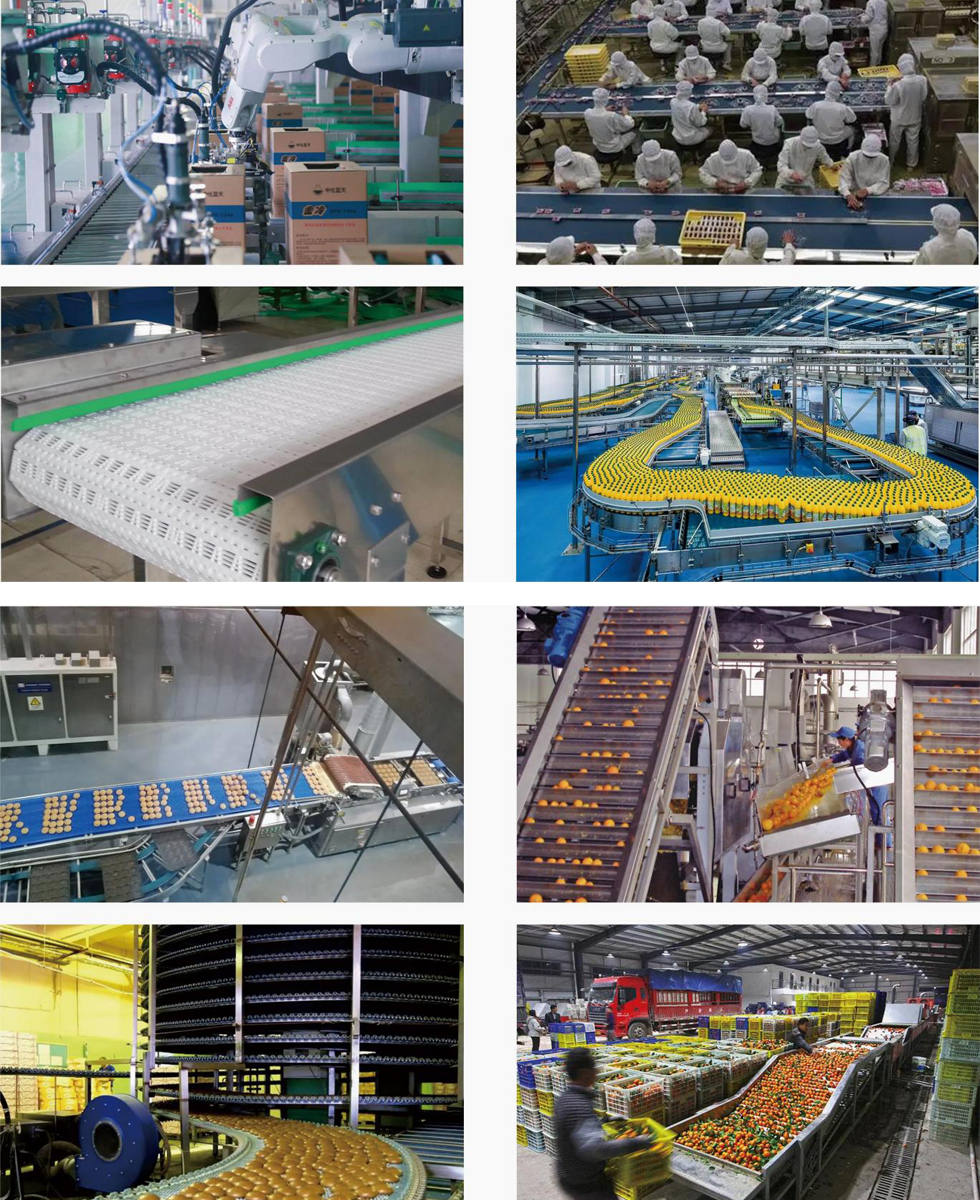
FAQ
1. Q:Are you a factory outlets or trading company?
A:We are a factory outlets.
2. Q:If small order is acceptable? Yes,trial order is welcome!
A:Yes,trial order is welcome!
3. Q:Could you offer us samples?
A:Yes, generally, free sample for 1~2pcs, and the freigt you need to bear.
4. Q:What’s your shipment terms?
A:Generally, if samples, by air or by express; If bigger order by sea.
5. Q:Could you put our logo on the packing?
A:Yes, it is easy to print your logo on the packing.
6. Q:What’s your package?
A:In standard export cartons, but could be designed as your request.
7. Q:What’s your main port of lading?
A:FoShan/GuangZhou/ShenZhen/ShangHai/NingBo.
Packaging and Shipping
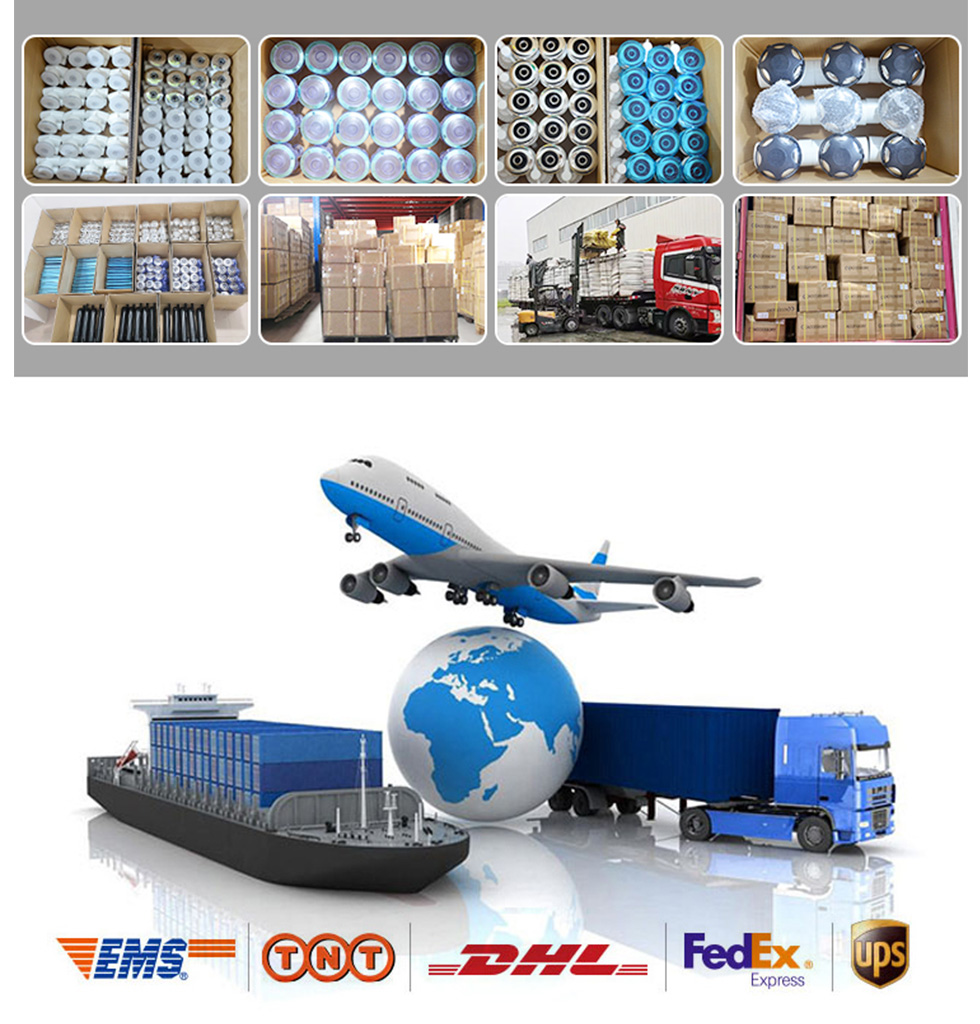
Certificates
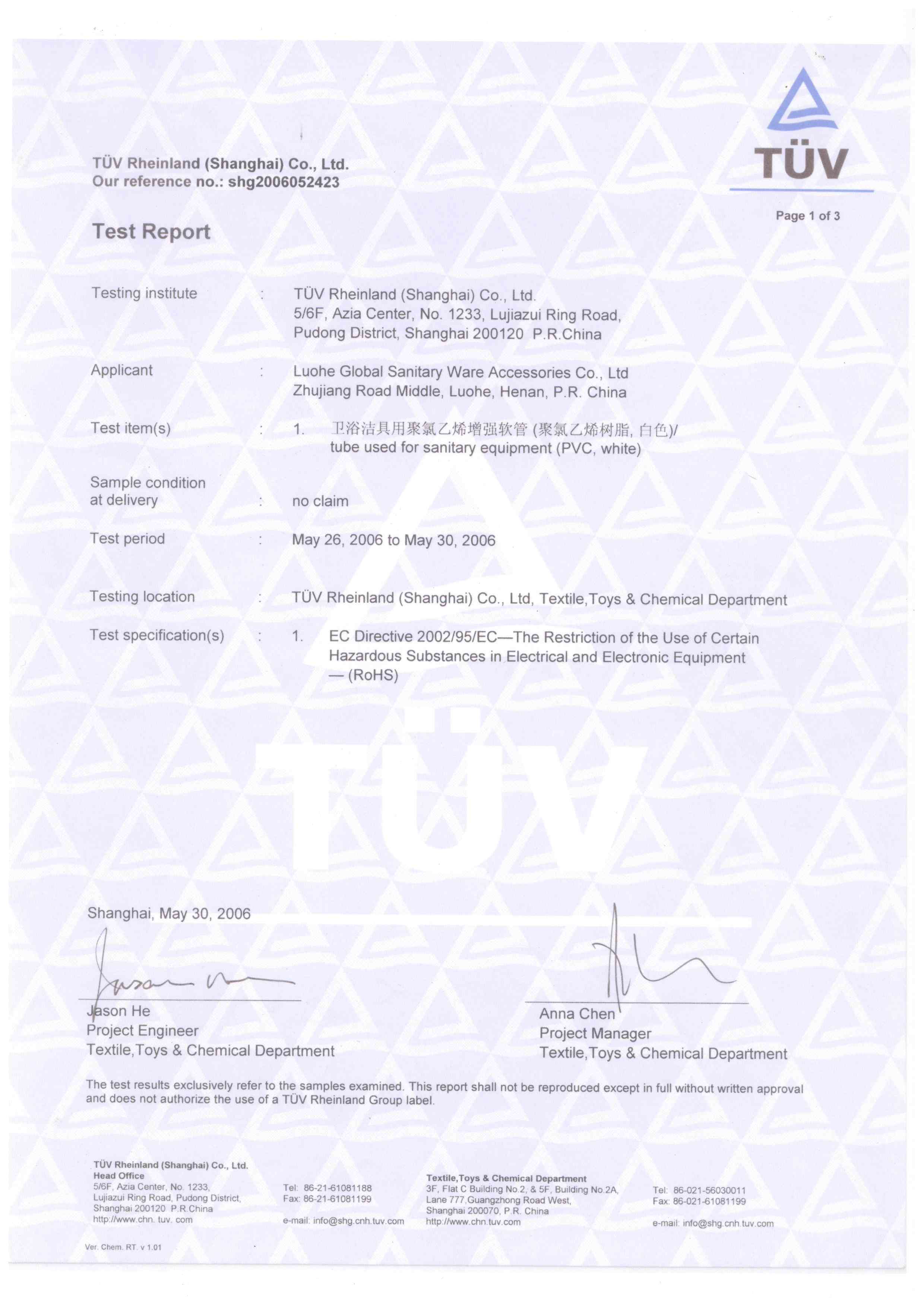
1.png)
3-213x300.png)
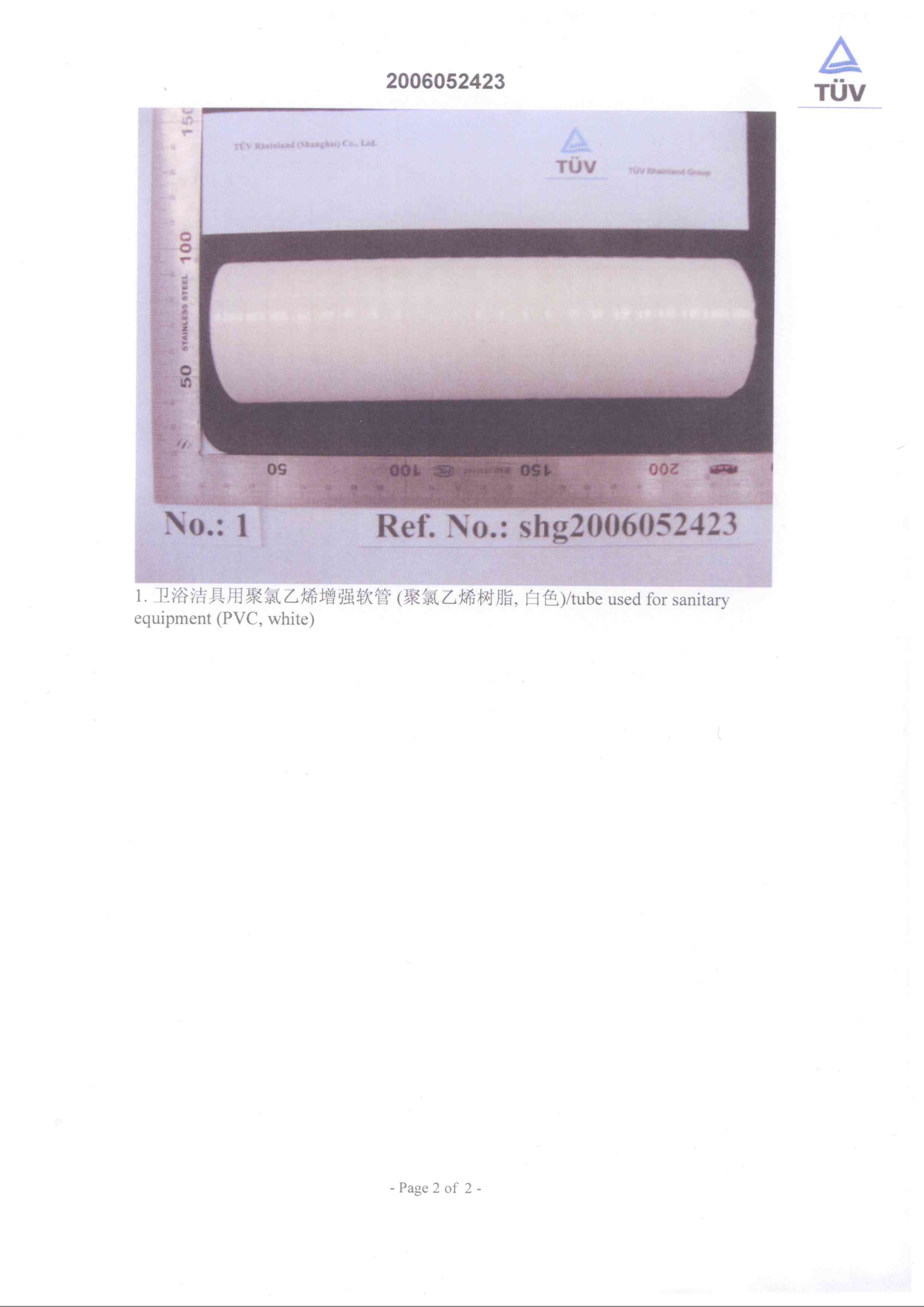
1.png)
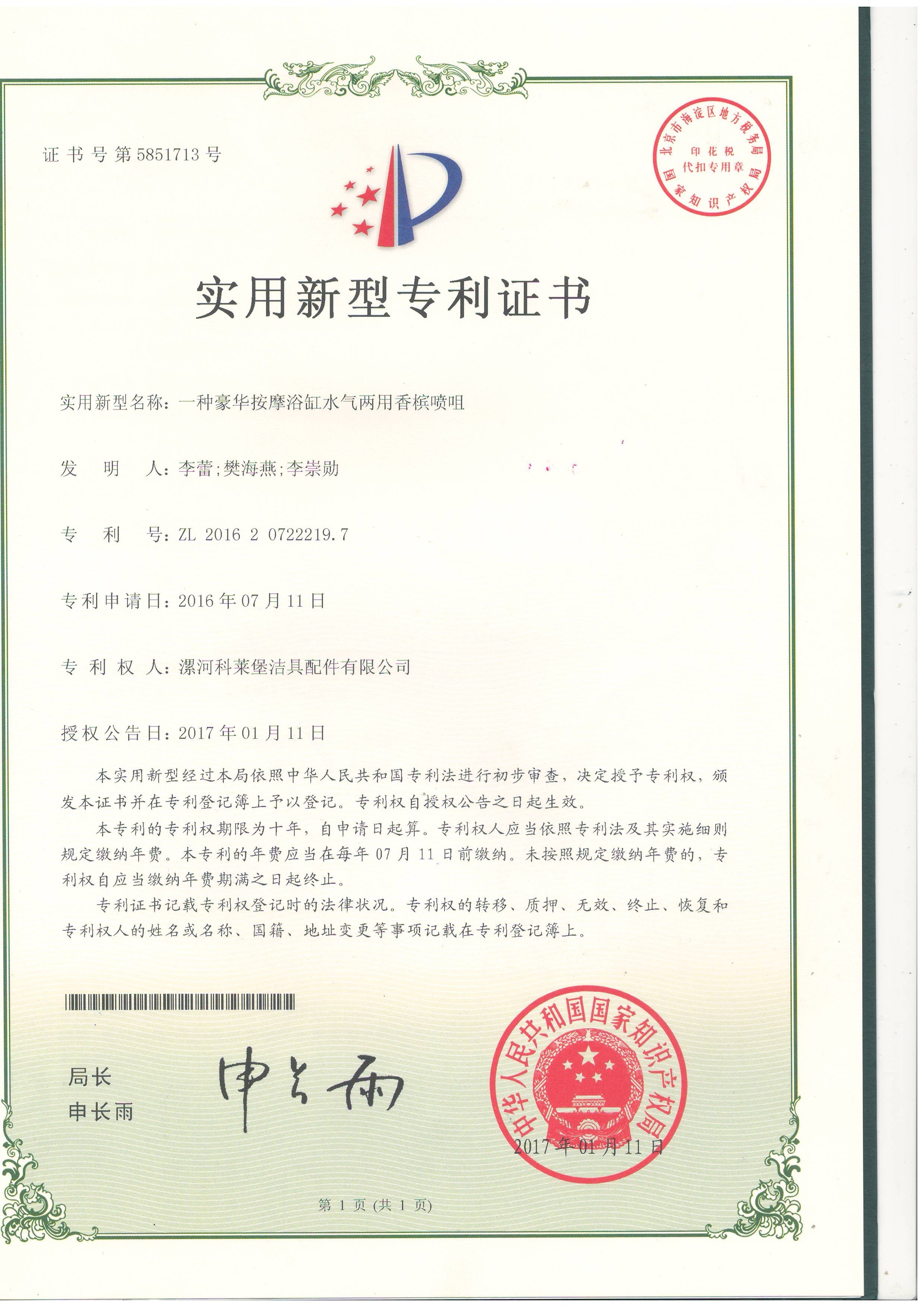
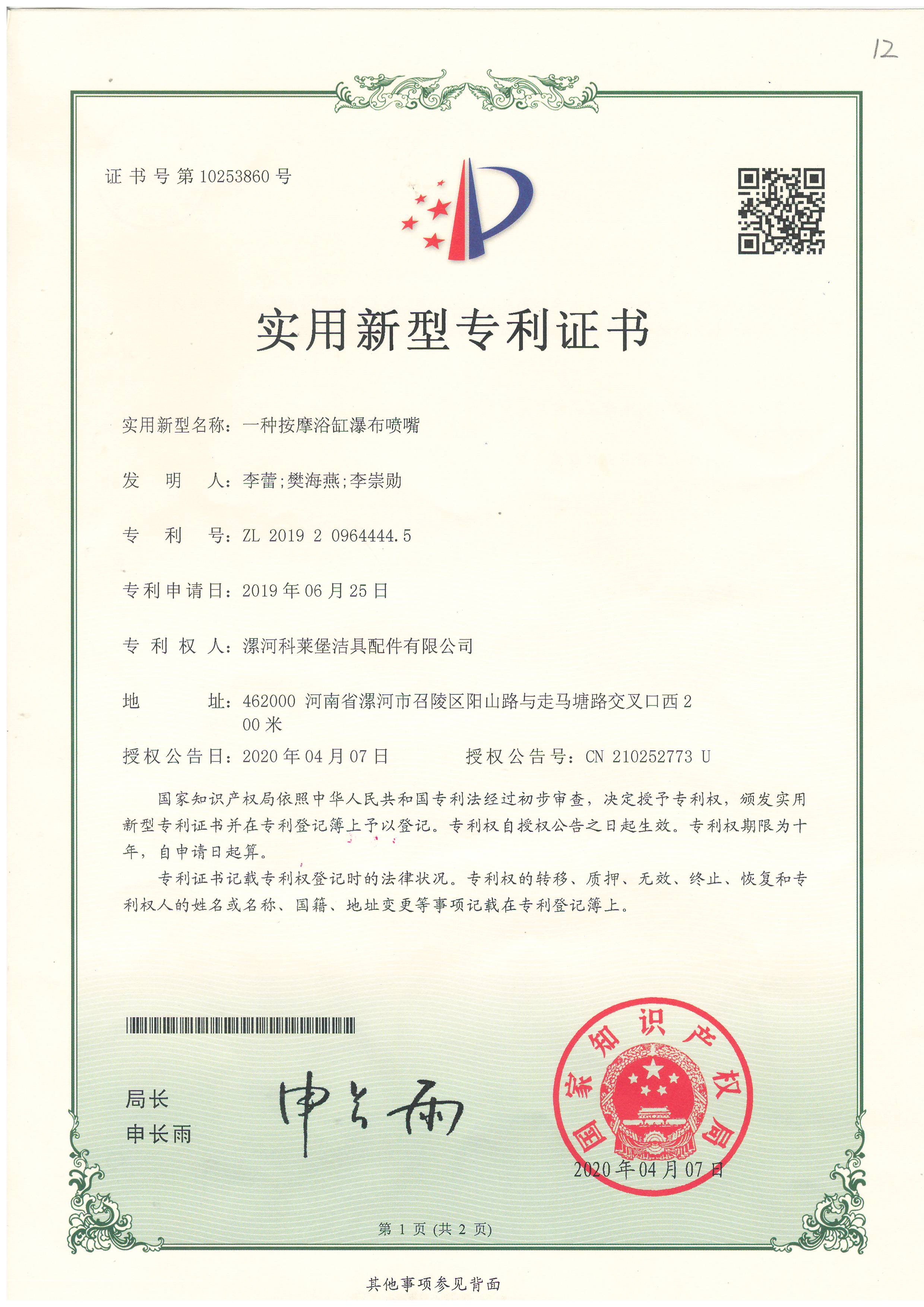
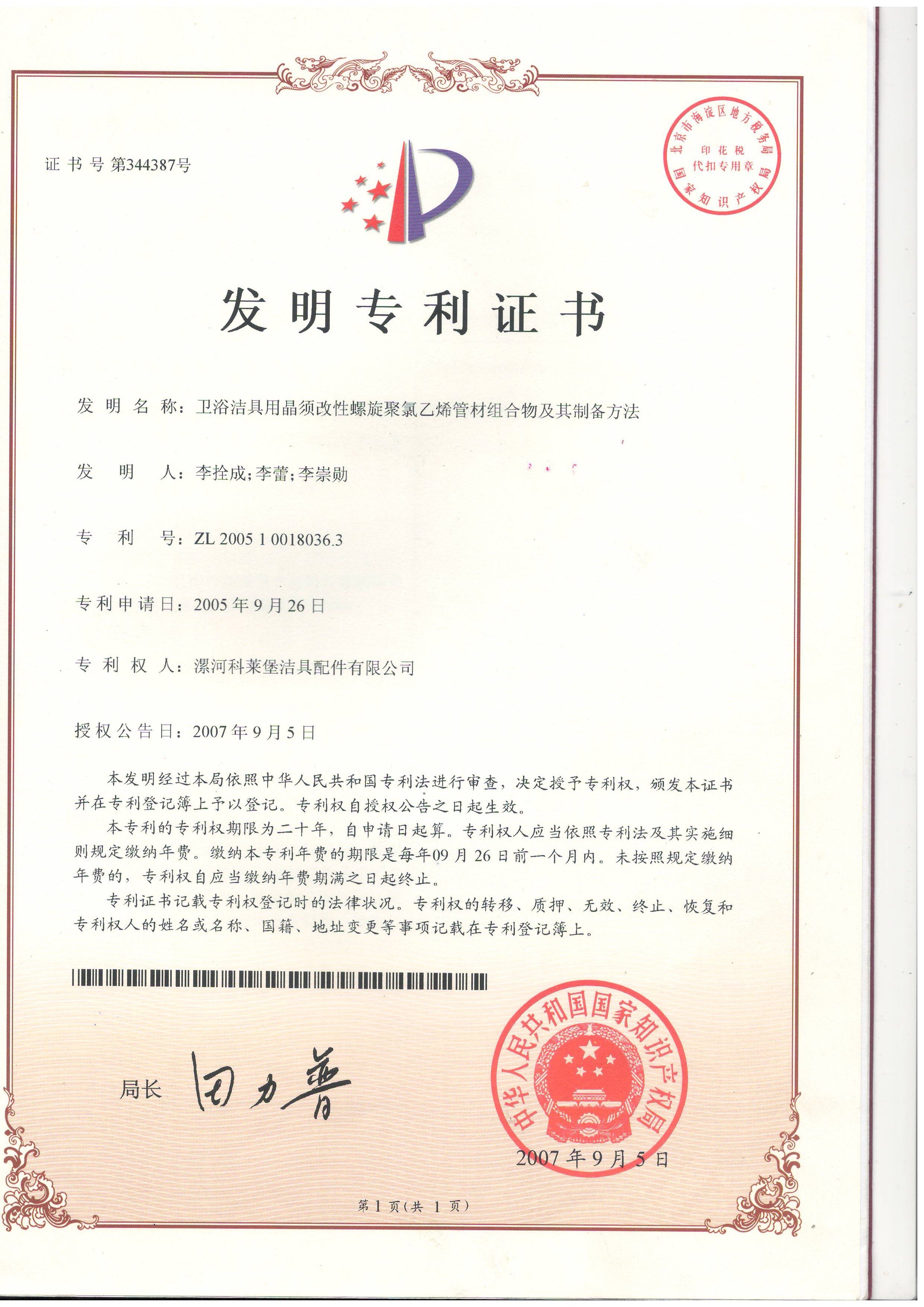
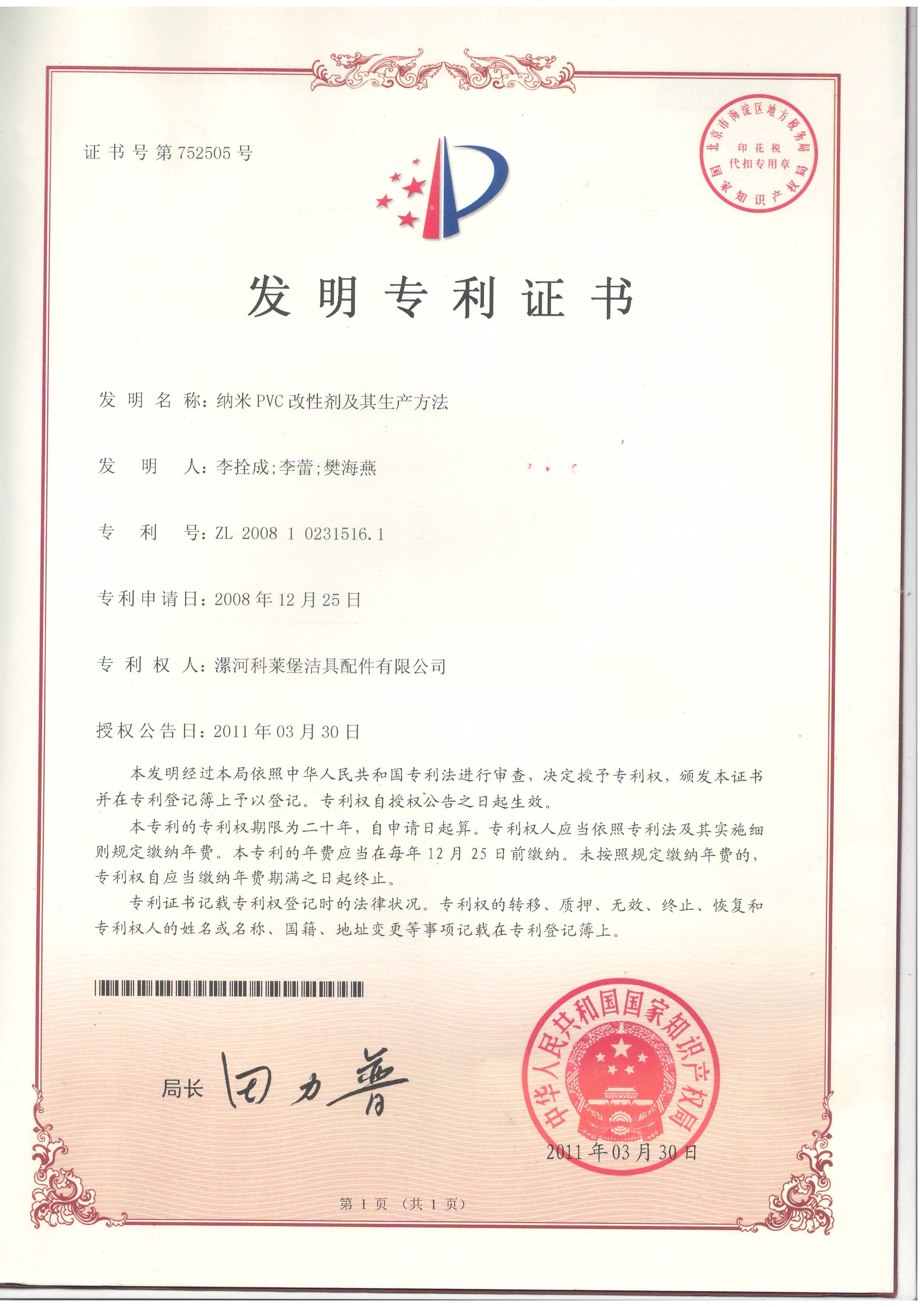
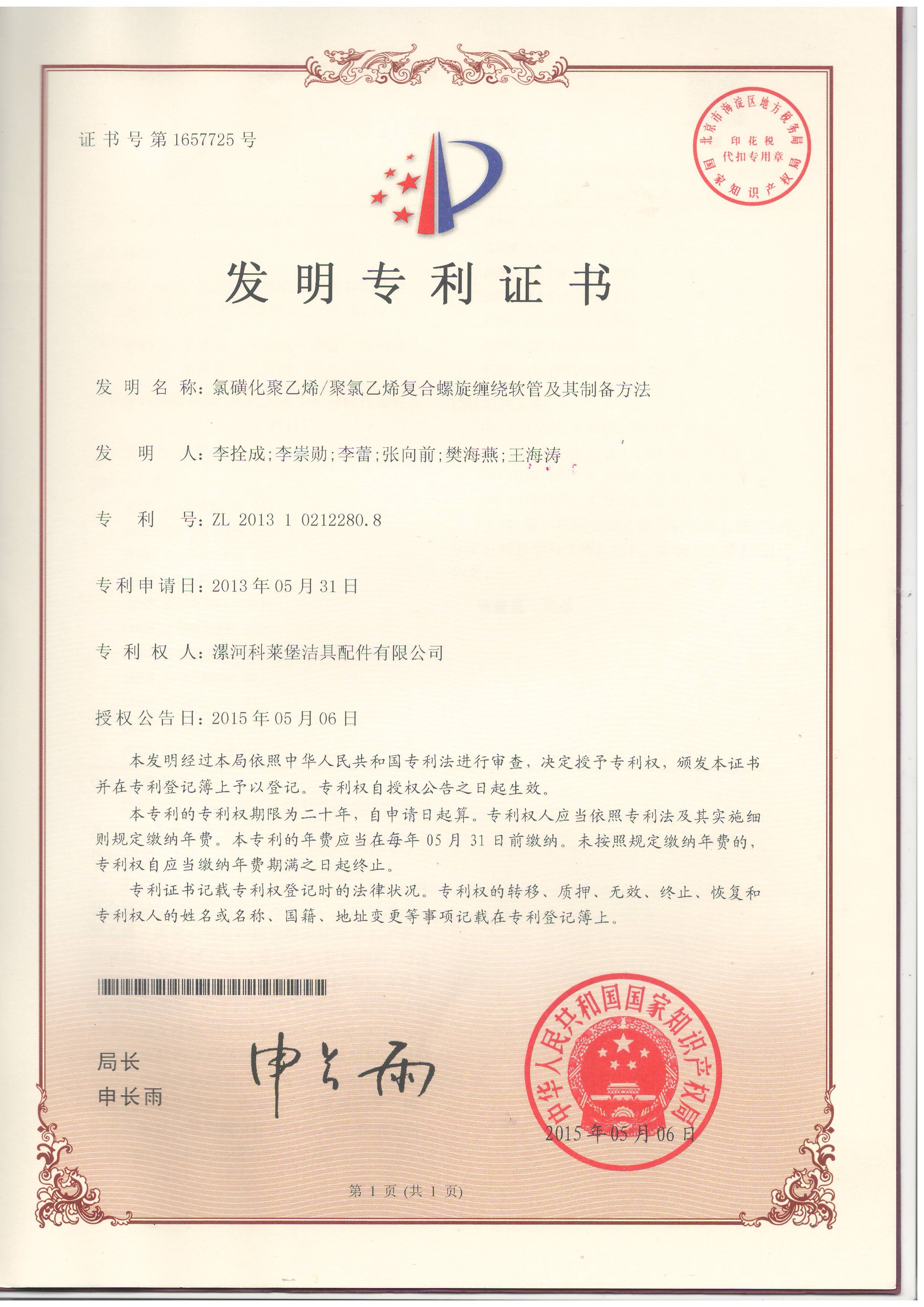
Customer Feedback
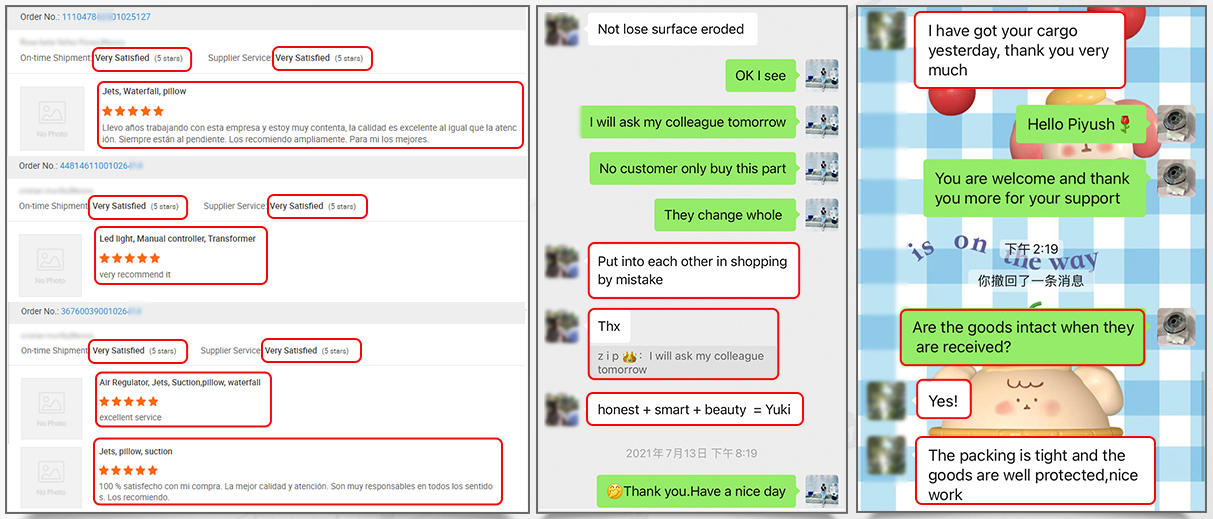
Photos of Exhibition Customers Collection
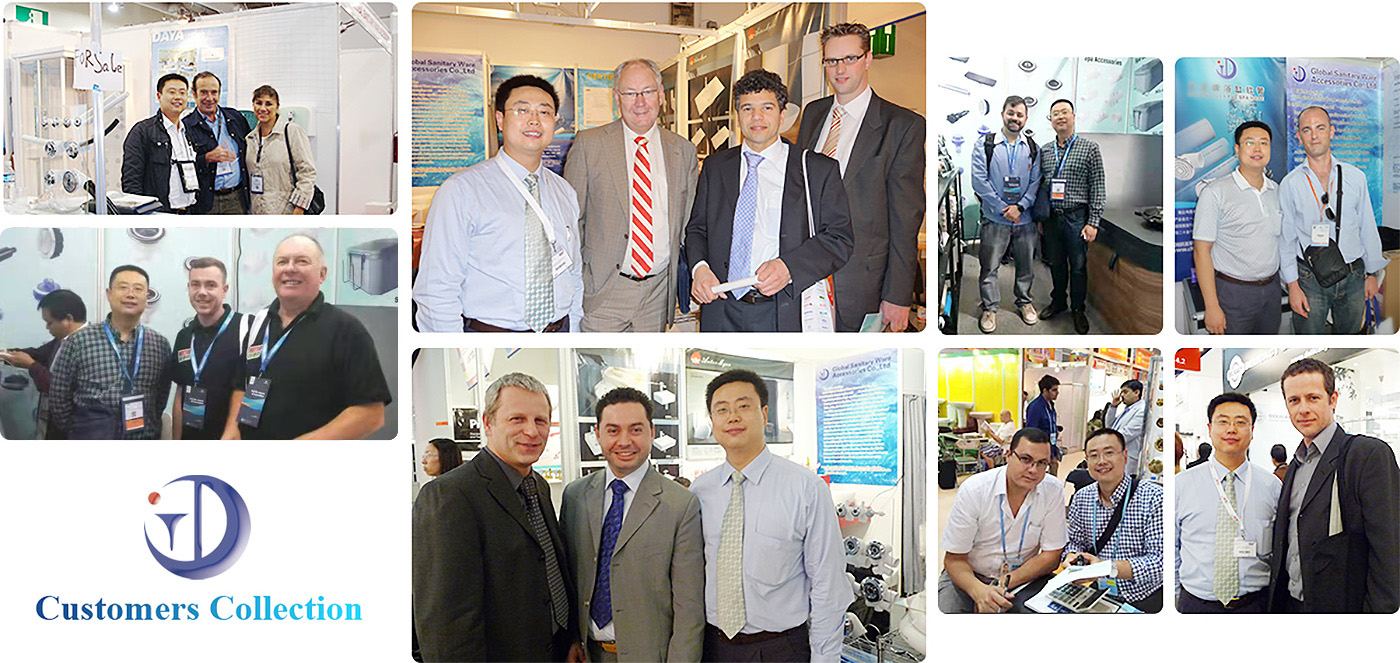
Welcome to Visit Our Factory
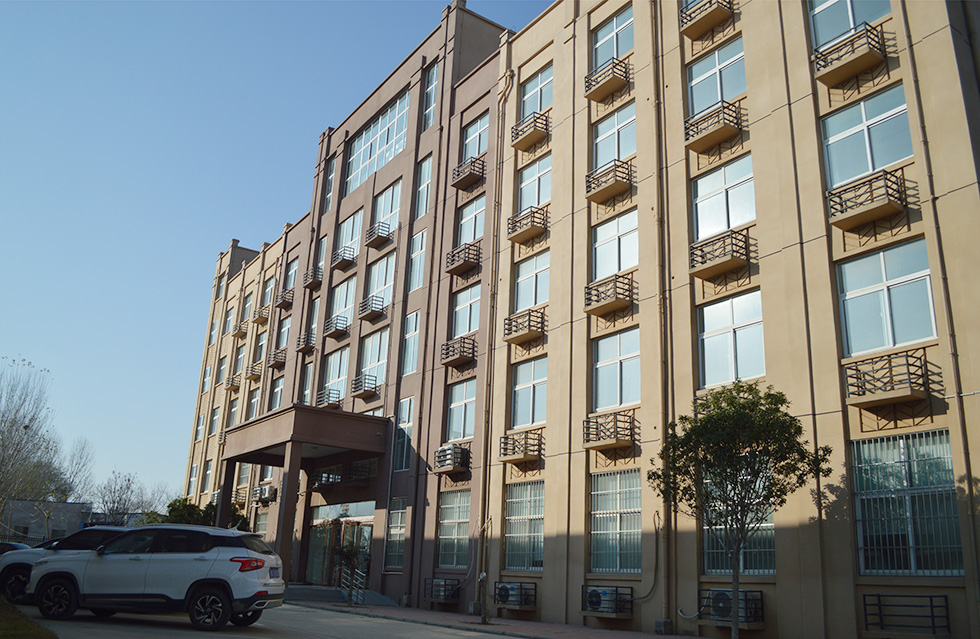
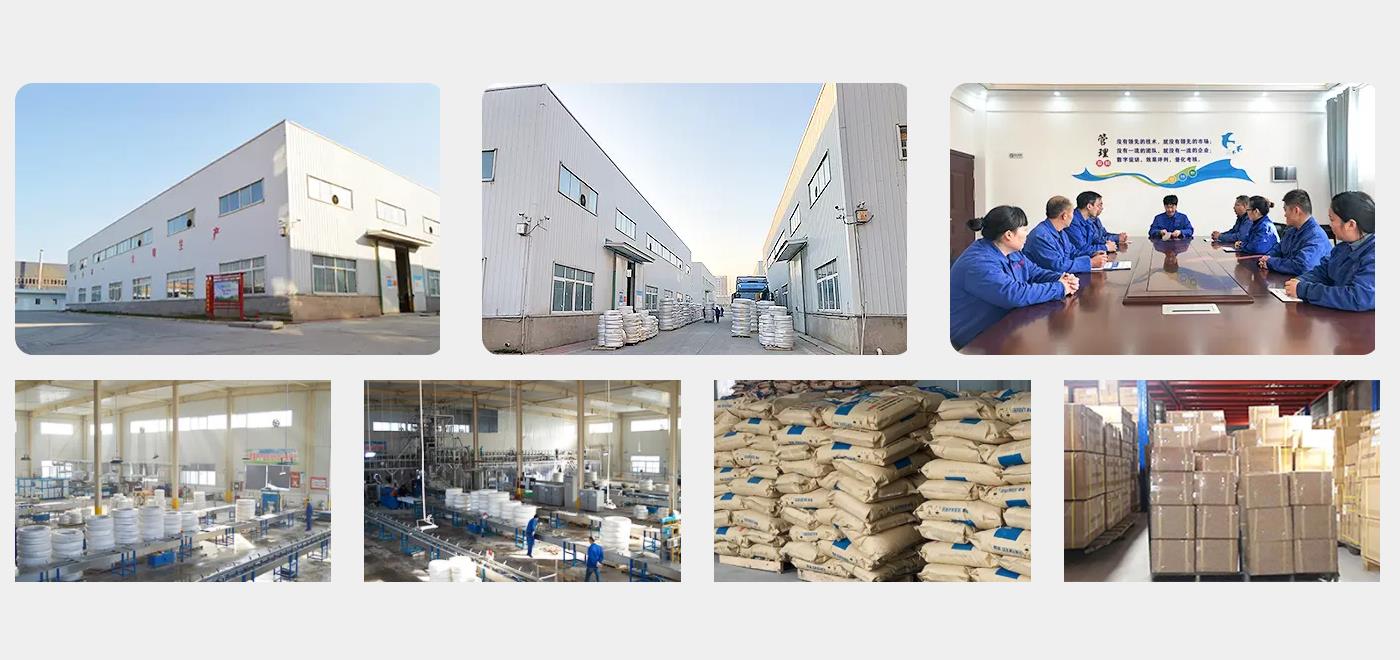
News
Wearing Strip, Wear Plates, and Wear Parts Information
Show all Wearing Strip, Wear Plates, and Wear Parts Manufacturers
Wear plates, Wearing Strip and wear parts are used to reduce wear or erosion in mechanical systems. They are used wherever abrasion, impact, or heat may cause wear and tear on mechanical components. The proper selection of Wearing Strip, plates and parts requires an understanding of both application requirements and product specifications.
Wear plates, Wearing Strip and wear parts include basalt or ceramic liners which protect manufacturing machinery from abrasion or impact. These specially-designed wear pads or linings are resistant to the abrasive effects of the bulk processing of grain, ore, salt, limestone, coal, glass, and fly ash. Other wear plates, strips and parts are made of bronze, chromium, tungsten, cast iron, or aluminum. A chromium wear plate is useful in harsh or severe environments because of its low coefficient of friction. Tungsten carbide wear plates are extremely wear resistant, as well as corrosion resistant. A tungsten carbide wear plate is used in mining applications, power generation, and cement manufacturing.
Uses
Wear plates, Wearing Strip and wear parts are used in bearings systems, foundry mold slides, and gas turbines. A bronze wear plate is commonly used as the flow divider plate in a gas turbine. Wear plates, strips and parts also include components made of plastics and polymers. Ultra-high molecular weight (UHMW) Wearing Strip are plastic films that can be bonded with an adhesive backing and attached to a variety of mechanical components, including bushings, bearings, blades, rails, liners, wipers, and guides. A UHMW wearing Strip comes in a variety of thicknesses and can be custom fit to specific machine parts.
Other wear plates, Wearing Strip and wear parts include self-lubricating parts for use on impact-activated hinged doors. A self lubricated wear plate enables the door to be opened repeatedly from both directions while minimizing the wear on the hinge. Impact-activated hinged doors are used frequently in high traffic areas such as warehouses, grocery stores, and medical centers.
Material handling processes often utilize machinery with many moving parts. After time, the points of contact between moving parts can wear down and cause disruptions in the workflow. Wearing Strip and components act as a sacrificial link in the system to prevent damage to the critical components of the equipment.
Wearing Strip and components are often made of plastic, which provides protection from surface marring and scratching, noise reduction between mating parts, and elimination of slipping and sticking amid sliding parts. One of the most common plastic materials used in wearing Strip applications is UHMW (Ultra High Molecular Weight Polyethylene). UHMW’s unique properties including high impact/abrasion resistance, self-lubrication, long wear life and ease of machining make it ideal for this application. Wearing Strip and components are resistant to corrosion and chemicals and able to keep moving parts free of external grease and lubricants. Wearing Strip and components are commonly used with bearings, slides, gears, cams, bushings, and rollers.
Demanding conveyor environments, such as biomass plants, cement works, pulp and paper factories or sawmills, rely on robust machinery that can consistently and reliably transport high volumes of material, often over long distances.
Efficient handling of those materials is essential for cost-effective production – and conveyor downtime, whether it’s as part of a scheduled preventative maintenance programme, or due to an unplanned outage, can have a detrimental effect on production capacity.
With so many moving parts within the conveyor system there are many possible points of contact where excessive friction can cause components to become worn.
So what can you do to keep your conveyor systems moving?
Increase efficiency
One simple way to protect critical components and prolong the wear life of your conveyor chain is through the use of a specialist thermoplastic wearing Strip.
And by choosing a wearing Strip that has been specifically produced for your style of conveyor chain it is possible to greatly extend chain wear life and increase operational efficiency.
By decreasing the coefficient of friction, the chain slides more easily and there is also the added benefit of reducing the amount of power that is needed to drive the conveyor.
The wearing Strip can be mounted onto your conveyor in a variety of ways. You may prefer to bolt it down to the conveyor directly. Or, if it is difficult to access, it may be preferable to mount it in a galvanised channel which will ensure that replacement is quick and easy.
Visual inspection
Visual inspections should always form part of your preventative maintenance schedule as they will save you time and maintain the best performance.
Sometimes the visual inspection of chains and wearing Strip can be difficult – especially if the components are located inside the conveyor system or in a harder-to-reach area.
One solution which can makes it easier to see when your wearing Strip needs replacing is a specially-designed wearing Strip that changes colour as it wears.A simple change in surface colour provides a clear visual indication that it is time to replace the wearing Strip.It is always advisable to change your wearing Strip before the chain starts to drag along the base of the conveyor.By monitoring and promptly replacing your wearing Strip you will preserve the integrity of your chain and conveyor – which will minimise production downtime and keep your running costs down.